Design of In line Blender
In-Line Blending
Blending Today
Many refineries and oil terminals are still blending components using a batch blending by sequential pumping to a tank. This means, pumping sequentially “n” components from blend component tanks to a final product tank.
Why In-Line Blending?
There are many advantages in using an in-line blender vs. sequential pumping components to a blend tank; for example:
- Reduce the blending time by at least 50%, which frees tanks for other purposes and allows for less inventory on hand
- Reduce octane and vapor pressure property giveaway within the limits of error or measurements
- No off-specs or re-blends
- Minimize demurrage charges
- Fewer/less testing of blend samples (saving $)
- Direct blending to ship or pipeline to reduce tankage and inventory
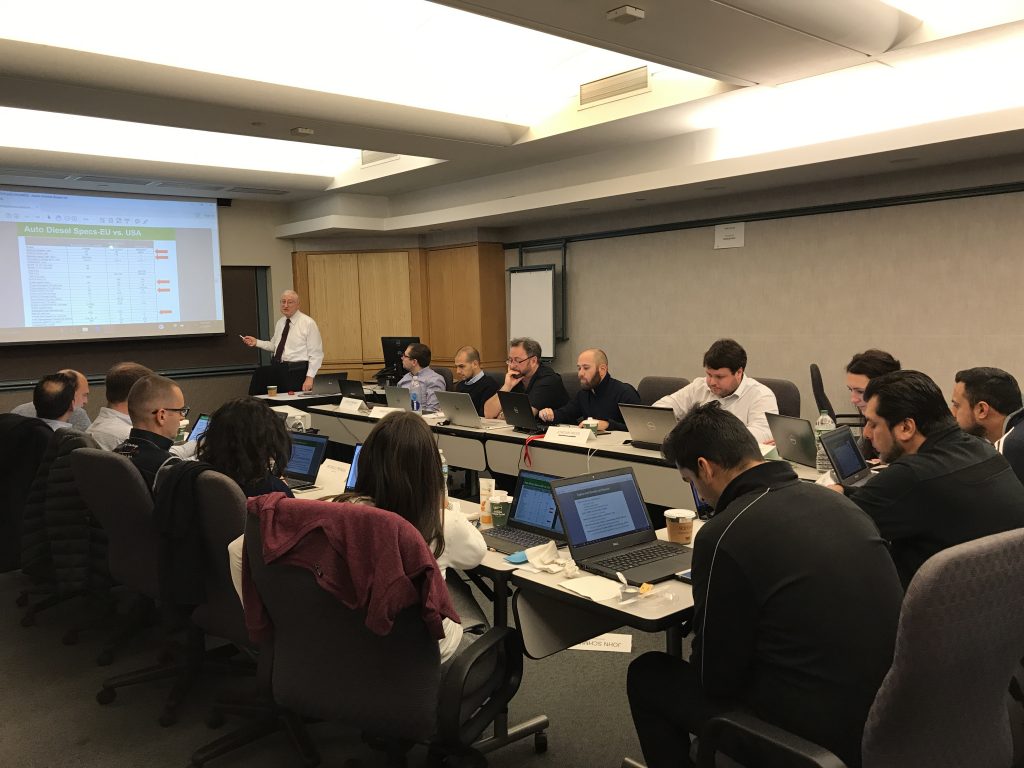
State of the Art In-Line Blending System
Refinery Automation Institute has been in the business for over 50 years, designing in-line blenders for gasoline, diesel, and bunker worldwide.
Save $-Money and switch to in-line blending. Switching to in-line blending will allow us to help you:
- Save money
- Increase tank farm throughput
- Automate and optimize the process
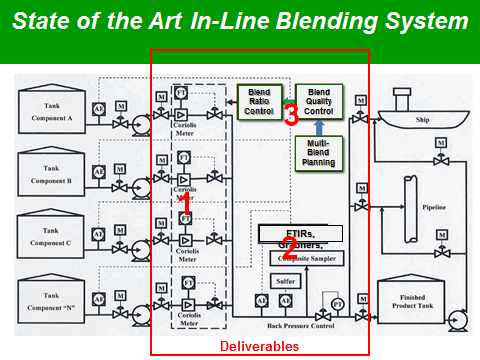
What We Provide
- A modular drop-In place skid-mounted, pre-wired, turn-key blender
- An analyzer shelter with pre-installed on-line analyzers
- Analyzers sampling system skids per ASTM practices
- Analyzer calibration check skids
- Blending control system using robust blend optimizer and on-line analyzer validity checking
- Installation assistance
- Blending personnel training
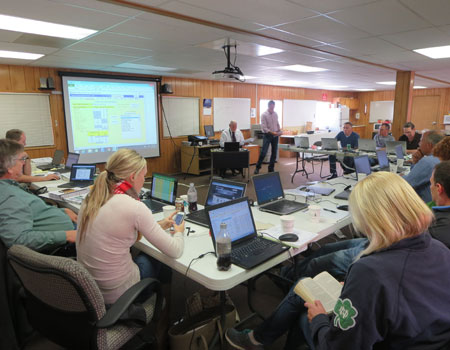